Masterbatch Usage: Common Errors and How to Avoid Them
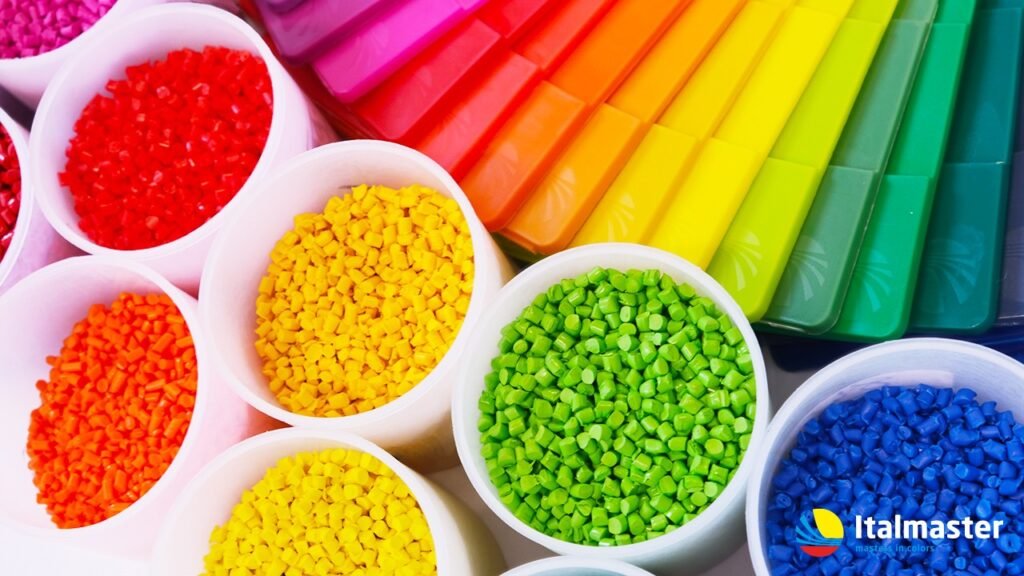
Masterbatch is an essential component in the plastics industry, widely used for coloring and enhancing plastic materials. However, if not handled properly, it can lead to issues in production quality and efficiency. In this article, we’ll explore some of the most common mistakes when using masterbatch and provide tips on how to avoid them. This will help ensure that you get the best results in your plastic products without compromising on quality.
1. Using Incorrect Dosage of Masterbatch
One of the most frequent mistakes in using masterbatch is miscalculating the required dosage. Adding too much or too little can cause inconsistencies in color and functionality, which impacts the appearance and performance of the end product.
How to Avoid This Mistake:
- Follow the manufacturer’s recommended dosage precisely.
- Conduct test runs to determine the optimal dosage.
- Use calibrated equipment to ensure accurate measurements.
2. Incompatible Masterbatch Selection
Using a masterbatch that isn’t compatible with the base polymer can lead to poor bonding, uneven coloration, and structural weaknesses in the final product. Each type of plastic requires a specific type of masterbatch for proper results.
How to Avoid This Mistake:
- Always verify compatibility between the masterbatch and the polymer before production.
- Consult with suppliers to ensure you’re using the correct type for your materials.
- Opt for a universal masterbatch only if you are certain of its compatibility.
3. Neglecting Moisture Control
Moisture is a major enemy in plastics production, as it can cause bubbles, streaks, and poor adhesion in products. Many types of masterbatch are sensitive to moisture and can degrade if not stored or handled correctly.
How to Avoid This Mistake:
- Store masterbatch in a dry, controlled environment to minimize moisture absorption.
- Use desiccant or drying agents to maintain low humidity levels.
- Pre-dry the masterbatch if needed, especially in humid climates or for hygroscopic polymers.
4. Incorrect Mixing Techniques
Improper mixing of masterbatch with raw materials can result in uneven distribution of color and additives. This mistake often arises from using low-quality mixing equipment or improper mixing parameters.
How to Avoid This Mistake:
- Use high-quality mixers or mixing machines that ensure even distribution.
- Regularly inspect and maintain mixing equipment.
- Follow best practices for mixing times and speeds to prevent under- or over-mixing.
5. Not Accounting for Processing Temperature
Masterbatch materials are sensitive to temperature changes, and processing them at the wrong temperature can lead to discoloration, degradation, or loss of desired properties in the final product.
How to Avoid This Mistake:
- Set processing temperatures according to the recommendations of the masterbatch and polymer manufacturers.
- Monitor temperature closely during production to ensure consistency.
- Avoid sudden temperature changes, which can cause thermal shock and damage the masterbatch.
6. Improper Storage and Handling of Masterbatch
Poor storage and handling can affect the quality of masterbatch, causing contamination or degradation over time. This is particularly problematic for long-term storage or in high-humidity environments.
How to Avoid This Mistake:
- Keep masterbatch in sealed containers, away from direct sunlight and moisture.
- Store in a clean, cool, and dry environment.
- Label and date each batch to ensure they’re used within the recommended timeframe.
7. Failure to Test and Monitor Consistency
Relying solely on initial setup without regular quality checks can result in issues down the line, especially when there are variations in production runs. Testing is crucial to ensure that the final product meets specifications consistently.
How to Avoid This Mistake:
- Conduct regular quality checks throughout the production process.
- Use standardized testing methods to measure color, texture, and durability.
- Adjust the masterbatch formulation or processing parameters based on the results.
8. Ignoring Safety Precautions
Masterbatch materials often contain concentrated pigments and additives that require careful handling. Ignoring safety precautions can put workers at risk and potentially contaminate the product.
How to Avoid This Mistake:
- Ensure all workers handling masterbatch materials use proper personal protective equipment (PPE).
- Follow handling and disposal guidelines as recommended by the supplier.
- Train staff on safe handling procedures and emergency protocols.
Conclusion
Avoiding these common mistakes when using masterbatch can help ensure high-quality results in your plastic production. By following these best practices—from choosing the right type and dosage to ensuring proper storage and handling—you can optimize your production process and enhance the quality of your final products. Attention to these details not only prevents costly errors but also ensures consistency, safety, and satisfaction for your clients and end-users.